Magnatech has delivered five ID welders to a contractor specializing in reworking critical valves used in electrical power plants.
Main Steam Isolation Valves (MSIV) are used to throttle the steam flowing into a steam turbine generator. These massive valves are critical for safety, and must close within seconds in the event of a steam line break. They also allow maintenance to be performed on the steam turbines.
Over time, the valve seats degrade due to thermal stresses, corrosion and other factors. These massive valves cannot be simply removed for maintenance in a workshop. They must be reworked in-situ. The valve actuator is removed, along with the top of the valve body. The valve seat is located 4-6’ below. A fixture is mounted on the top of the valve. This locates the machining tool precisely to machine out the original valve seat, which is usually stellite material.
The machining tool is removed, and a weld overlay system mounted on the precision fixture. An overlay of Inconel 625 material is made which requires repetitive overlapping passes, and a number of layers. A video camera allows the operator to view the weld area. The valve seat area is shaped like the “bell” on a trumpet. The torch can be quickly angled to keep it 90 to the valve body, as it moves from bottom to top of this “bell” (see photo.) The welding Head is designed so that the function of the Arc Voltage Control and torch cross seam adjustment slides can be interchanged with a switch on the Head.
Following sufficient weld buildup, the weld Head is removed, and the machining tool reinstalled to cut the weld buildup into the precise geometry of a new valve seat.
What began as a request to improve existing equipment, turned into replacing most of the system. The contractor had already replaced power sources from
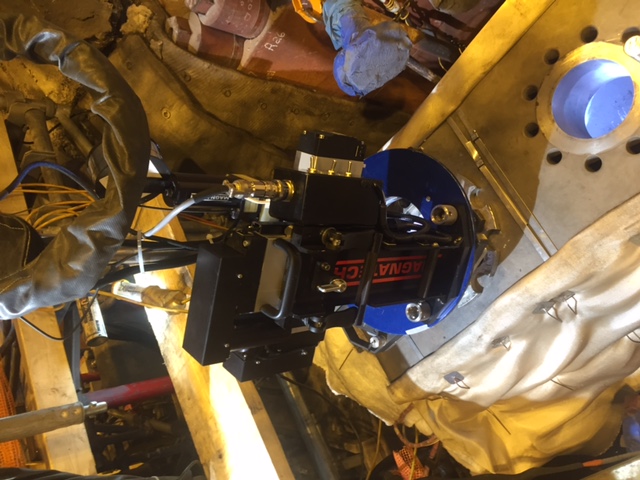